Paul Reed Smith ~ポール・リード・スミスについて~ その50 (生産プロセス17)
前回はこちら。
https://www.niconico-guitars.com/html/blog/staffblog/paul-reed-smith-49/
バフがけが完了した後は、”Turn Around”(ターン・アラウンド)と呼ばれるクオリティチェックの工程に入ります。
PRS創設当初はバッフィングルームから出てきたギターを検品のために並べられるラックが1つだけだったそうです。
チェックをしてから、
問題の無いギター→アッセンブリーエリアのある向きに変える
問題のあるギター→バッフィングルームのある向きにのままにする
文字通り”Turn Around = 向きを変える”というやり方だったそうで、現在もその方法は変えず、なんともアナログな方法でチェックしています。(分かりやすいとは思いますが)
これまでに多数のスタッフによるチェックが入れられ続けられていたギター達ですが、驚くことにターンアラウンドでは相当数の修正箇所(主に塗装)をあぶり出しています。
修正箇所は白いペンでギターに直接マークされます。
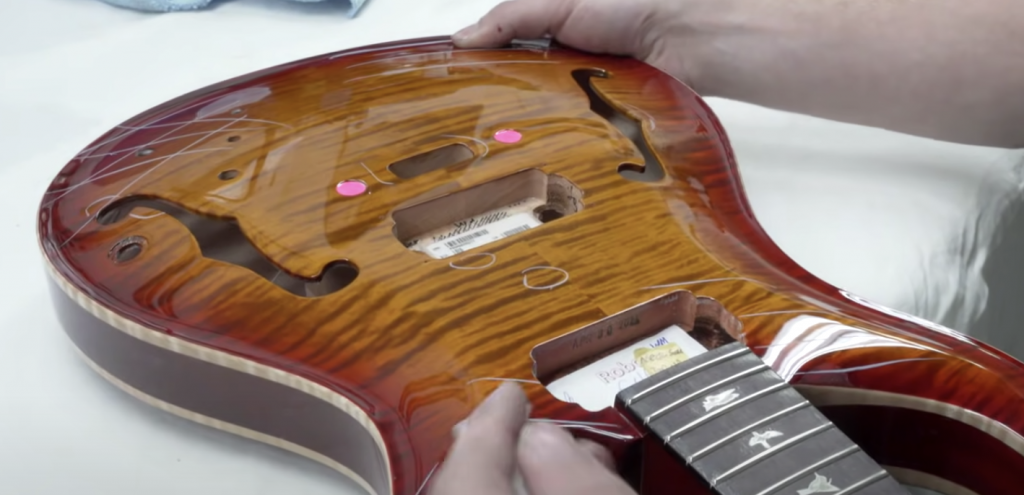
写真を見てもお分かりの通り、非常に沢山の修正箇所が。。。。
バフがけが甘い箇所、バフがけによるスクラッチ、フレットのバリ、塗料が厚くなってしまっている部分等、様々な理由で検品をクリア出来ず、修正がかけられていきます。
修正が完了し、本当に最終のバフがけが完了したギターは、このままアッセンブリールームに行くと思いきや、さらなるチェックが入ります。
さすがにしつこいとも思えますが、ここにもポール氏のクオリティに対しての徹底した信念が感じられますね。
指板の導管に入り込んだ塗装の粉(バフがけした時に飛び散ったもの)の除去や指板へのオイルの塗布などが行われて、とうとうアッセンブリーエリアへと向かいます。
と、ここでアッセンブリーエリアに向かう前にエレクトリックルームへ。
エレクトリックルームではピックアップ等のパーツ類全般の製造を行われています。
PRSではFenderなどとは異なり、所謂ハンドワウンドではなく、コイルを巻く大きな特注のマシーンを使ってピックアップを作っています。
ちなみにワインダーマシンは”Marsilli”というコイル・モーター専門の機械を生産するイタリアのメーカーで製作されたものをPRSでは使用しており、一度に4つのワインディングが可能です。
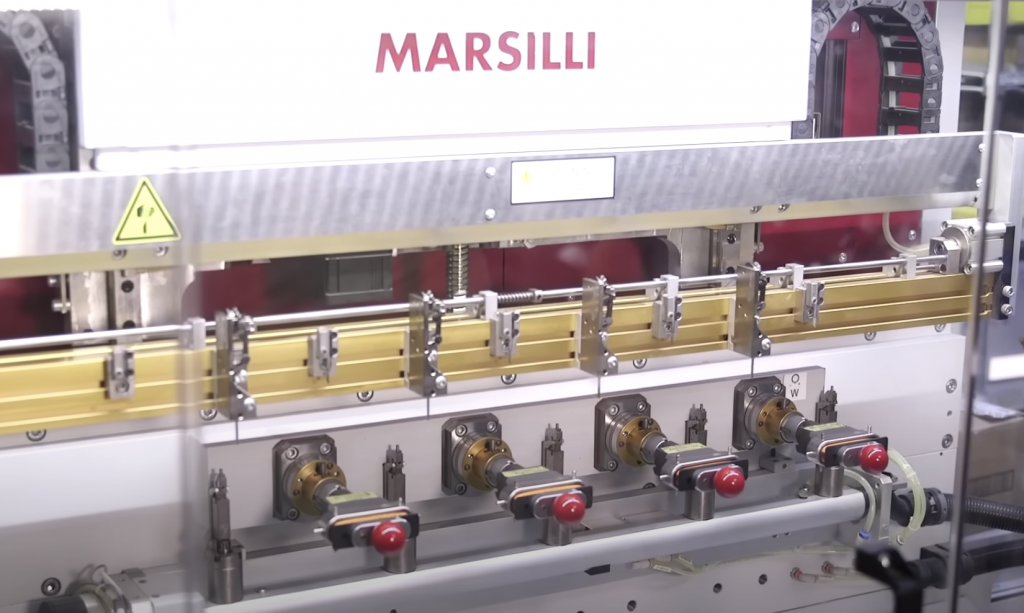
またボビンやプラスチック部分などの小さな部品は別会社に発注して作成したものを使用しています。
ワインディングが完了したピックアップは、リード線やプレートが付けられます。
その後にはピックアップを溶かしたパラフィン(蝋)に漬けるポッティング処理(ロウ漬け)へ。
PRSのピックアップのほとんどがハウリング対策とピックアップ自体の保護のためのポッティング処理が施されています。
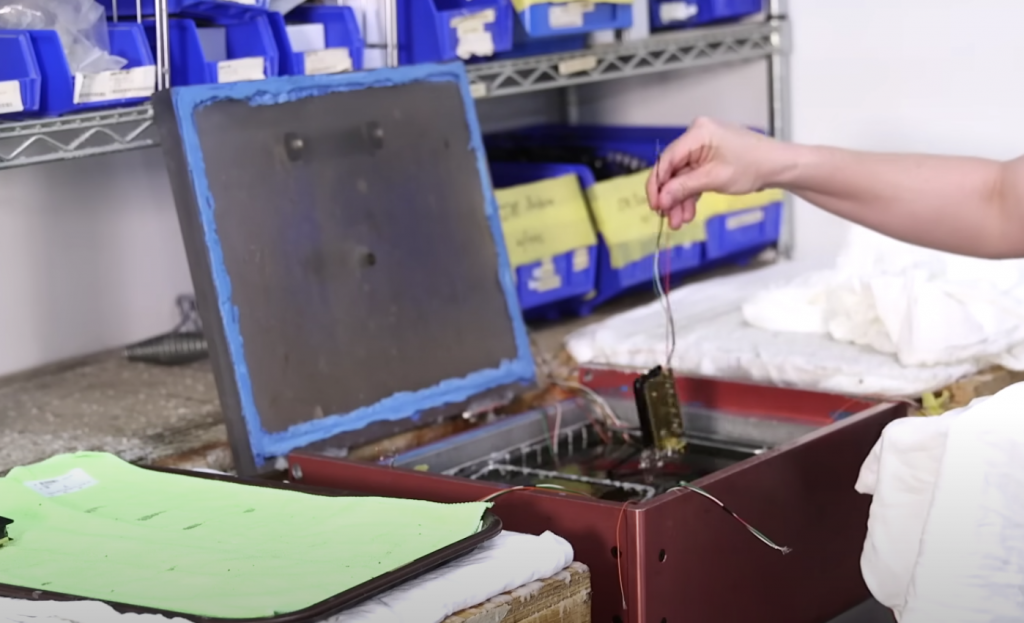
そうして完成したピックアップは抵抗値のチェックやラベリング(シール貼り)を経て、スイッチやポットなどの他パーツと共に”キットルーム”へと運ばれ、ギターへの搭載の最終準備へと移ります。
~続く~